- Overview
- Analysis Service
- Hot Service
- Investigations
- Techniques
- Advantages
- Cases
- Customer Reviews
- Latest Updates
- Online Inquiry

What is Material Failure Analysis?
Material failure analysis plays a crucial role in modern industry and scientific research. Its core focus is to investigate the performance degradation, damage, or fracture of materials during use, identify the root causes of failure, and implement corresponding improvement measures to optimize product performance and enhance material reliability.
Ensuring Safety and Reliability
Material failure can lead to equipment malfunctions, accidents, and even threaten human life. For example, the fracture and corrosion of metal materials can cause serious consequences such as bridge collapses or airplane crashes. Through failure analysis, potential issues can be detected in advance, preventive measures can be taken, and the safety of products and systems can be ensured.
Optimizing Design and Processes
Failure analysis reveals the failure modes and mechanisms of materials in specific environments, providing scientific evidence for improving designs and optimizing manufacturing processes. For instance, in the automotive industry, in-depth analysis of failure causes can lead to adjustments in part structures, enhancing the vehicle's performance and durability.
Reducing Costs and Increasing Efficiency
Through failure analysis, companies can minimize the economic losses caused by material failures, avoid product recalls, and reduce repair costs. At the same time, optimizing material selection and usage conditions can improve production efficiency and resource utilization.
Driving Technological Innovation
Failure analysis provides data support for the research and application of new materials. For example, by studying the failure behavior of composite materials in different environments, more durable materials can be developed.
How We Conduct Material Failure Analysis






- Microstructure Analysis
- Mechanical Property Testing
- Chemical Composition Analysis
- Surface Morphology Characterization
- Fracture Surface Analysis
- Corrosion and Wear Behavior Studies
Microstructure Analysis
Using equipment such as Scanning Electron Microscopes (SEM) to observe the microstructure of materials, identifying issues like cracks, defects, and corrosion.
Mechanical Property Testing
Assessing the material's performance under different conditions through tests such as tensile, compression, and impact tests to help analyze the causes of failure.
Chemical Composition Analysis
Using methods like X-ray Diffraction (XRD) and Energy Dispersive Spectroscopy (EDS) to evaluate the material's composition and check whether it meets the required standards.
Surface Morphology Characterization
Surface morphology analysis involves using high-resolution microscopy techniques (such as SEM) to observe the material's surface features. By analyzing the surface morphology, we can determine whether there are scratches, corrosion, fatigue cracks, or other phenomena present on the material's surface.
Fracture Surface Analysis
Analyzing the fracture surface of the material to identify the fracture type (e.g., brittle, ductile fracture) and its cause.
Corrosion and Wear Behavior Studies
We conduct studies on the corrosion and wear behaviors of materials, analyzing their corrosion resistance and wear resistance under different environments and working conditions. By simulating corrosion or wear processes in real-world working environments, we help predict the material's long-term performance and provide data support for improving material protection strategies.
What Types of Materials We Work With

Metal Materials
Metal materials are one of the key subjects in failure analysis. Common metal materials include steel, aluminum alloys, copper alloys, and others. The failure modes of metal materials are diverse, including fracture, corrosion, fatigue, wear, etc. Failure analysis methods include microstructure analysis (such as metallographic analysis, X-ray phase structure analysis), composition analysis, fracture analysis, residual stress analysis, and more. For example, the failure of metal materials may be caused by factors such as poor design, improper material selection, manufacturing defects, or improper heat treatment.
Metal Materials

Polymer Materials
Polymer materials also play an important role in failure analysis. Their failure modes include cracking, delamination, corrosion, discoloration, and more. Failure analysis methods include composition analysis, thermal analysis, mechanical property testing, etc. For example, the failure of polymer materials may be related to factors such as chemical exposure, environmental stress, and manufacturing defects.
Polymer Materials

Ceramic and Composite Materials
Ceramic materials and composite materials have wide applications in fields such as aerospace and biomedical industries. Failure analysis involves various techniques, including nondestructive testing, composition analysis, mechanical property testing, and more. For example, failure modes of ceramic matrix composites include fiber fracture, matrix cracking, interlaminar delamination, etc.
Ceramic and Composite Materials

Semiconductor and Electronic Materials
Failure analysis of semiconductor materials and electronic components is an important research direction in modern technology. Failure modes include electromigration failure, open-circuit failure, short-circuit failure, and more. Failure analysis methods include scanning electron microscopy (SEM) analysis, reliability testing, Failure Modes and Effects Analysis (FMEA), and others. For example, the failure of semiconductor devices may be related to manufacturing defects, environmental stress, improper usage conditions, and more.
Semiconductor and Electronic Materials
Looking for Popular Failure Analysis Services?
When conducting material failure analysis, we focus on identifying the specific modes of material failure.

Fracture failure
Such as brittle fracture and ductile fracture, which typically occur when the material is subjected to stress beyond its capacity to withstand.

Corrosion failure
Due to chemical reactions or environmental factors, the surface of metals may undergo oxidation or corrosion, leading to material failure.

Wear failure
Related to friction, typically occurring on the surfaces where two materials come into contact.

Fatigue failure
Cracks or fractures occur in materials under long-term repetitive loading, commonly observed in mechanical components.
Key Components of Defective Material Investigations
When conducting material failure analysis, investigating the key elements of defective materials is crucial. These elements help us systematically identify and address the root cause of material failures. Below are the key factors to focus on when conducting a defective material investigation:

Material History and Usage Conditions
Understanding the history and usage conditions of a material is essential for investigating defective materials. Factors such as the environment of use, loading conditions, temperature, humidity, and chemical media can all impact the material's performance. For example, metals in high-temperature environments may undergo oxidation, and corrosive components in chemical media may lead to localized failure of the material.
Material Selection and Specifications
The selection and specifications of the material itself are fundamental factors in failure. If the material chosen does not meet the application requirements or is specified improperly, it can lead to premature failure. For defective material investigations, it is necessary to check the chemical composition, mechanical properties, production processes, etc., to ensure they meet design requirements.
Failure Modes and Fracture Analysis
Analyzing failure modes helps determine the source of defects. For instance, brittle fracture, fatigue fracture, and corrosion damage are failure modes that can help pinpoint the specific causes of material failure. Fracture analysis is key to understanding failure modes, revealing how, where, and why the failure occurred.
Microstructure and Physical Properties
The microstructure of a material significantly affects its performance, and defects often manifest as structural issues at the microscopic level. Using microscopy techniques (such as scanning electron microscopy), we can analyze key features such as grain structure, grain boundaries, defects, and phase composition, and assess whether there are any structural weaknesses present.
Mechanical Property Evaluation
Mechanical properties are critical indicators of whether a material can withstand real working conditions. By conducting tensile, compression, hardness, fatigue, and impact tests, we can analyze whether the material’s mechanical properties meet the required standards. If mechanical performance is lower than expected, it may indicate defects in the material itself or during the manufacturing process.
Chemical Composition and Corrosion Analysis
Chemical composition analysis helps identify whether there are elements or impurities in the material that could affect its performance. Corrosion behavior analysis reveals how the material performs in specific environments and whether corrosion is a contributing factor to failure. Types of corrosion (e.g., pitting, uniform corrosion) can also provide clues to the failure cause.
Environmental and Process Effects
The performance of materials can vary significantly under different environmental conditions. Factors such as high temperature, humidity, and salt spray may accelerate material degradation. Therefore, investigating environmental conditions is crucial in defect material analysis. Similarly, manufacturing processes (such as welding, casting, and heat treatment) may introduce microscopic defects that affect the material's reliability.
Multi-factor Analysis of Failure Causes
Material failure is often the result of multiple factors acting together. A single factor may not fully explain the failure, so multi-dimensional analysis is needed to accurately identify the problem. For instance, interactions between the material’s chemical composition, microstructure, mechanical properties, and environmental conditions may collectively lead to failure.
Failure Reverse Engineering and Comparative Analysis
By conducting reverse engineering of failed components, we can compare them with normal parts to identify differences, which helps uncover the root cause of the failure. This process involves not only physical and chemical analysis but also a comprehensive review of raw materials, manufacturing processes, and usage conditions.
Solution and Improvement Recommendations
The ultimate goal of defective material investigation is to identify the root cause of failure and propose effective improvement measures. These solutions may involve material replacement, process adjustments, or other remedial actions to prevent similar issues from occurring in the future.
Through in-depth investigation and analysis of these key factors, we can gain a comprehensive understanding of the causes of material failure and provide customers with scientifically sound and effective solutions to optimize material performance and reliability.
What Techniques Are Used in Material Failure Analysis?
Material failure analysis is a complex and multidimensional task that involves the integration of various techniques and methods. Below are some commonly used material failure analysis techniques that help identify the root cause of failure and provide a basis for material improvement and optimization:

Scanning Electron Microscope (SEM)
The Scanning Electron Microscope (SEM) is a key tool in material failure analysis and is widely used for fracture surface analysis. It provides high-resolution surface morphology images and, through additional energy-dispersive X-ray spectroscopy (EDX), can obtain information about the elemental composition. SEM can reveal the initiation points of cracks, the crack propagation paths, and microscopic defects on the material's surface, such as voids, inclusions, and more.

Transmission Electron Microscope (TEM)
The Transmission Electron Microscope (TEM) is used to observe the crystal structure and phase composition of materials, allowing in-depth analysis of the internal microstructure. TEM provides atomic-level structural information at high resolution, making it suitable for analyzing internal defects and failure modes in metals, ceramics, polymers, and other materials.

X-ray Diffraction (XRD)
X-ray diffraction (XRD) is used to analyze the crystal structure, phase composition, and stress state of materials. In failure analysis, XRD can help identify phase changes in materials, such as corrosion in metals or changes in precipitate phases, thereby aiding in determining the cause of material failure.

Energy Dispersive Spectroscopy (EDS or EDX)
Energy Dispersive Spectroscopy (EDS or EDX) is typically used in conjunction with SEM to analyze the elemental composition of a sample's surface or fracture region. This technique helps identify the material's components, impurities, and corrosion products. It is particularly useful for analyzing the chemical composition of materials and their distribution, revealing the underlying causes of corrosion or other chemical reactions.
How Our Expertise Sets Us Apart?

Experienced Expert Team
We have a team of senior engineers and material scientists with years of experience in material failure analysis.

Precise Testing and Analysis Equipment
We use advanced testing equipment such as Scanning Electron Microscopes (SEM), X-Ray Diffraction (XRD), and mechanical performance testing devices to ensure the accuracy of our analysis results.

Efficient and Accurate Result Reporting
We provide detailed analysis reports that help customers quickly understand the failure causes and offer a basis for further product improvements.

Customized Solutions
Based on the unique needs of each customer, we offer tailored failure analysis solutions to meet the specific requirements of various industries and products.
How Material Failure Analysis Can Help Your Industry?
Aerospace
In the aerospace field, material failure analysis is primarily used to assess design flaws, component failure modes, and system safety in aircraft and spacecraft. Through failure analysis, issues in the design or manufacturing processes can be identified, ensuring the safety and reliability of the aircraft.
Automotive Manufacturing
In the automotive manufacturing industry, material failure analysis is mainly used to identify potential design flaws in components and systems, ensuring the safety and reliability of vehicles.
Electronics and Semiconductors
In the electronics and semiconductor industry, material failure analysis is a key tool for ensuring product quality and reliability. Failure analysis helps identify failure modes of electronic components (such as short circuits, open circuits, corrosion, etc.) and determine their root causes.
Medical Devices
In the medical device industry, material failure analysis is crucial for ensuring the safety and effectiveness of equipment. Failure analysis can identify device failures due to design flaws or manufacturing issues, and measures can be taken to prevent similar problems from occurring.
Energy and Power
In the energy and power industry, material failure analysis is primarily used to assess potential failure modes of equipment and systems, ensuring the stability and safety of energy supply.



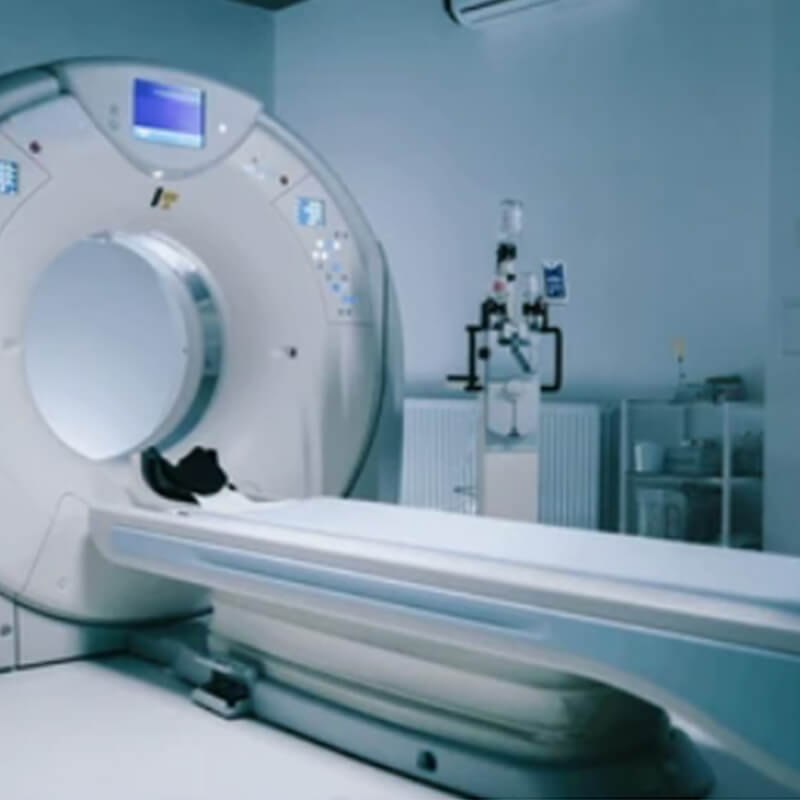

Aerospace
Automotive Manufacturing
Electronics and Semiconductors
Medical Devices
Energy and Power

What Success Stories Can We Share?
Here are three case studies showcasing failure analysis services conducted for other companies, highlighting the value and impact of our expertise.
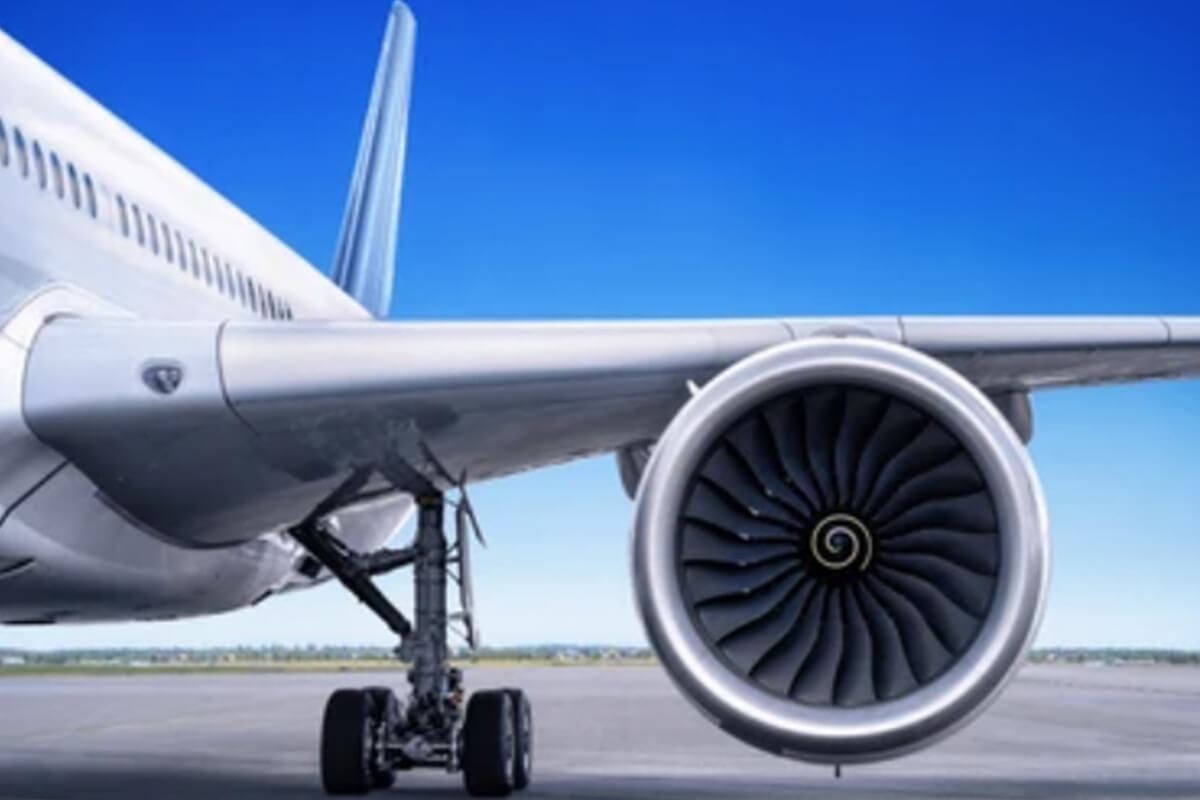
Case 1: Failure Analysis and Improvement Plan for Aircraft Engine Component Fracture
Background:
A certain airline company discovered frequent fractures in an aircraft engine accessory during regular flights. Upon inspection, the fracture occurred in a critical load-bearing component, severely affecting flight safety. The company contacted our laboratory for failure analysis to determine the cause of the fractures and provide an effective improvement plan.
Analysis Process:
We first performed a microscopic analysis of the fracture surface using Scanning Electron Microscopy (SEM) and found that the fractures exhibited distinct brittle characteristics. The crack initiation point was located at a small internal defect in the material. Next, we conducted mechanical property tests and found that the material's tensile strength was insufficient to withstand high-load environments. Through further chemical composition analysis, we discovered the material contained excessive sulfur and phosphorus, which could contribute to increased brittleness.
Solution:
Based on the analysis, we recommended replacing the original material with a high-strength, low-sulfur alloy and enhancing the heat treatment process during production to improve toughness and fatigue resistance. Additionally, we suggested applying a corrosion-resistant coating to the material surface to prevent corrosion cracks in high-temperature environments.
Outcome:
After replacing the material and optimizing the manufacturing process, the airline company reported that the fracture issue was effectively resolved, and the component's lifespan and reliability were significantly improved. The company indicated that the optimized components performed far beyond expectations in actual use, reducing the risk of flight downtime.

Case 2: Wear Failure Analysis and Material Optimization for Automotive Engine Components
Background:
A certain automotive manufacturer discovered excessive wear in key components of a new engine during long-term operation tests. This issue not only affected engine efficiency but also led to increased energy consumption. The company decided to entrust us with failure analysis to determine the cause of the wear and provide a solution.
Analysis Process:
We conducted wear resistance tests on the components using a wear testing machine, and found that wear primarily occurred at the friction contact surfaces, with the wear rate significantly exceeding design standards. Scanning Electron Microscopy (SEM) of the worn surfaces revealed numerous microcracks and spalling. Combining mechanical property tests and chemical composition analysis, we found that the material's hardness and wear resistance were inadequate, causing gradual failure of the material's surface under high-temperature, high-load conditions.
Solution:
We recommended using an alloy with higher hardness and optimizing the surface treatment process, such as utilizing nitriding or chrome plating to increase surface hardness and wear resistance. Additionally, we suggested reducing the temperature rise at the friction contact surfaces by optimizing the cooling system design to extend the component's lifespan.
Outcome:
After material optimization and process improvements, the wear rate of the engine components significantly slowed, energy efficiency improved, and the components' lifespan was greatly extended. The automotive manufacturer reported no further wear issues in subsequent use, and the overall performance of the engine improved.
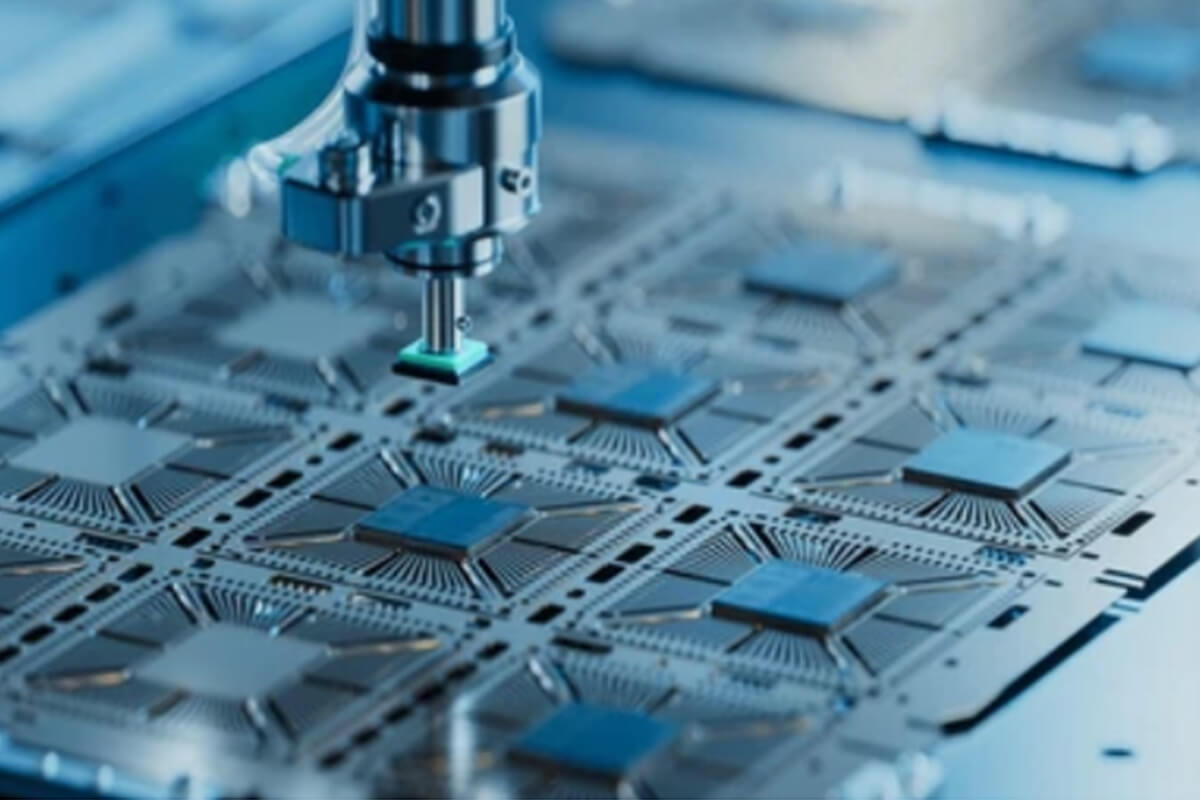
Case 3: Corrosion Failure of Electronic Packaging Materials and Protective Measures
Background:
A certain electronics manufacturer discovered serious corrosion issues with their packaging materials during use, leading to decreased stability of the electronic products and even short-circuit failures. To identify the root cause of the issue and propose protective measures, the manufacturer contacted our laboratory for detailed failure analysis.
Analysis Process:
We conducted surface morphology analysis of the packaging materials and found that corrosion was concentrated at the material’s contact and welding areas. Energy Dispersive X-ray Spectroscopy (EDX) revealed the formation of an oxide layer on the surface, and the corrosion was due to the combined effects of humidity and high-temperature environments. Further corrosion behavior testing showed that the packaging materials were subjected to significant environmental corrosion during prolonged use of the electronic products.
Solution:
We recommended using more corrosion-resistant packaging materials, such as ceramic or modified polymer materials, and strengthening the sealing process during packaging to prevent moisture ingress. Simultaneously, we suggested applying a corrosion-resistant coating to enhance material durability and improving the thermal stability of the packaging materials to ensure that the electronic products would remain stable during extended use without corrosion issues.
Outcome:
After replacing the materials and optimizing the packaging process, the corrosion issue of the electronic products was effectively controlled. The new packaging materials enhanced the corrosion resistance of the electronic products, ensuring stable operation even in high-temperature, high-humidity environments. The manufacturer expressed satisfaction with the improved product performance, reducing maintenance costs and enhancing the product's market competitiveness.
What Our Clients Say?

Latest Updates
Stay informed with the latest updates from our company, where we continually innovate and enhance our services to meet your needs.
- All
- Application Notes
